福建耐用不锈钢砂轮片采购
发布时间:2024-10-15 00:59:04
福建耐用不锈钢砂轮片采购
砂轮打磨原本采用是单齿面与多齿面打磨,单齿面打磨砂轮虽然加工精度较高,但打磨的效率非常低,成本很高,多齿面打磨砂轮虽生产效率高,但是其加工质量比单齿打磨差很多。 好的效果是采用CBN砂轮打磨,因为具有以下优势:1.CBN砂轮寿命长,打磨性能好,节约了砂轮更换修整、机床调整和工件检测等许多辅助时间。2.可以制成精度较高的齿形,由于耐用度高,不频繁修整,不需经常调整机床,可获得稳定的齿廊、导程和节距精度。3.可实现高速打磨与高进给率打磨齿面,粗糙度低且不会烧伤,可在提高打磨效率的条件下获得较高的齿轮精度(6~7级)。采用,无论采用单齿面打磨还是采用多齿面打磨,采用电镀CBN砂轮或陶瓷结合剂砂轮进行打磨,其效果极为显著。

福建耐用不锈钢砂轮片采购
找出通过砂轮中心的下位置点A;第二步:与A点在同一直径上的对应点做一记号B;第三步:加入平衡块C,使A.B两点位置不变;第四步:再加入平衡块D.E,并仍使A和B两点位置不变。如有变动,可上下调整D.E使A,B两点恢复原位。此时砂轮左右已平衡;第五步:将转动90度。如不平衡,将D,E同时向A或B点移动,直到A.B两点平衡为止;如此调整,直至能在任何方位上稳定下来,砂轮就平衡好了。根据砂轮直径的大小,检查6个或8个方位即可。
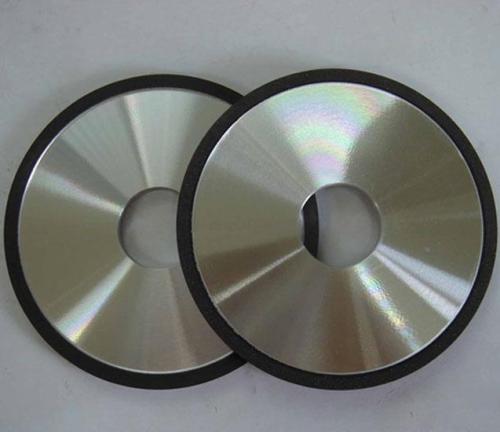
福建耐用不锈钢砂轮片采购
钨钢砂轮平衡支架是磨床必须配备的附件,大家应该了解它的原理,在以后的使用中可能会用到。钨钢砂轮不平衡的砂轮在高速旋转时会产生振动,影响加工质量和机床精度,严重时还会造成机损坏和砂轮碎裂. 引起不平衡的原困主要是砂轮各部分密度不均匀,几何形状不对称以及安装偏心等。 砂轮平衡支架选用材料作平衡轴,经热处理以及精密的加工与装配故而精度高,性能稳定是一理想的机床附件。一般直径大于125mm的砂轮都要进行平衡,使砂轮其旋转轴线重合。钨钢砂轮因此在安装砂轮之前都要进行平衡,的平衡有静平衡和动平衡两种。一般情况下,只需作静平衡,但在高速磨削(速度大于 50m/s)和高速度磨削时,必须进行动平衡。平衡时将砂轮装在平衡心轴上,然后把装好心轴的砂轮平放到砂轮平衡支架的平衡导轨上,会作来回摆动,直至摆动停止。平衡的砂轮可以在任意位置都静止不动,如果砂轮不平衡,则其较重部分总是转到下面,这时可移动平衡块的位置使其达到平衡。

福建耐用不锈钢砂轮片采购
磨削时应使砂轮轴线与工件轴线等高,以保证球面的圆度。通常可根据磨削花纹来判断等高性的误差。如被磨球体表面呈凸状花纹,表明砂轮的下半周参加磨削,即砂轮的的中心低于工件中心,此时,应调整砂轮的中心位置,使之与工件中心等高,直至被磨球体表面呈交叉网状花纹。其误差要求在0.003-0.004mm之内。外球面时,砂轮架要转动角度,故砂轮内孔尺寸的修整应在机床调整前完成。砂轮在磨削过程中磨钝后,不需要修整内孔,只要用砂条修整砂轮的端面即可,这样既能使砂轮恢复锋利,又可保证砂轮的内孔尺寸不变。砂轮磨钝后要及时修整,以利于保证加工质量。由于球面轴线与工件轴线不可能等高,这样工件上会产生一个很小的台阶,影响工件精度,此时,可在球面顶端钻一个小于1mm的中心孔来避免。

福建耐用不锈钢砂轮片采购
(1)玻璃材料:各种玻璃管、玻璃壶口、茶漏、高硼硅玻璃、米珠、毛细玻璃管、光学玻璃、石英玻璃、微晶玻璃、宝石、水晶、玉石;(2)陶瓷材料:氧化铝、氧化锆、碳化硅、碳化鹏、氮化硼、黑陶瓷、琉璃制品;(3)研磨材料:耐火材料、超精油石;(4)磁性材料:磁芯、磁片、磁环、永磁铁氧体、稀土钕铁硼;(5)合金材料:高速钢、模具钢、合金钢、不锈钢;(6)脆金属材料:YG系列硬质合金,钨钢圆棒。(7)半导体材料:碳化硅、硅片、单晶硅、多晶硅、太阳能电(8)光学材料:LED、LCD、石英光伏。
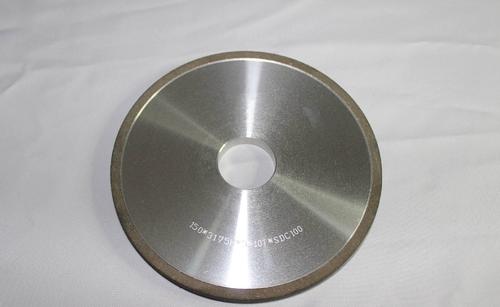
福建耐用不锈钢砂轮片采购
选择电镀金刚石砂轮硬度的一般原则是:加工软金属时,为了使磨料不致过早脱落,则选用硬砂轮。耐磨性强、寿命长。CBN砂轮磨削比可达3500—5500,比普通刚玉砂轮高百倍,比金刚石砂轮高3—5倍。加工硬金属时,为了能及时的使磨钝的磨粒脱落,从而露出具有尖锐棱角的自锐性,选用软砂轮。后者是因为在磨削软材料时,砂轮的工作磨粒磨损很慢,不需要太早的脱离;后者是因为在磨削硬材料时,磨损较快,需要较快的更新。工作效率高、综合经济效益好。磨削锋利、磨削力小、CBN砂轮修整周期长、修整量较少、更换时间长;使用周期长,磨削比高,可获得较佳的经济性,使用中形状保持性好,无需经常更换砂轮和修整砂轮,节约工时,改善劳动条件,有利于加工操作。